 |
|
Double Column Milling Center |
|
Slant Bed CNC TEACH-IN Lathe |
|
Turning Milling CNC Lathe |
|
|
|
TS Series Slant Bed CNC TEACH-IN Lathe |
|
- Machine & technology
- Technology & Options
- Controls
- Specifications
- Floor Plans
The new slant bed CNC TEACH-IN lathe from ARIX
gives extraordinary machining capacity, stability and precision. |
The specially designed structure enhances the heavy cutting capabilities
and easy operation TEACH-IN controller makes the quick and simple setup
and programming.
|
Heavy duty Meehanite Cast Bed
The optimal structure is ribbed for maximum stiffness.
The gray cast iron offers excellent damping properties and Meehanite process ensures the casting is
properly heat treated and annealed before aging.
The homogenized casting is free from any stress concentrations that can withstand any heavy-duty cutting.
45°slant bed construction assures solid support of turret and efficient chip removal.
Hand Scrapped Box side ways
The Cast-in slide-ways generates the maximum rigidity.
The heat treatment by high frequency induction heating produces a depth of 0.5 mm maximum wear
resistance structure with tough internal core.
The precise & fine hand scrapping on all contact surfaces ensure the accuracies are held throughout
machine life.
|
High rigidity, High Precision Spindle
The spindle is encased in the ribbed headstock for maximum heat dissipation.
The thick cast iron case can damp all the vibration from cutting.
For spindle configuration, the angular thrust bearings to absorb axial cutting forces and the roller
bearings with large bearing areas facilitate heavy cutting capacity.
Fast indexing, durable turret
The turret has Curvic coupling for high positioning accuracy and the hydraulic clamping for heavy cutting.
The fast indexing with bi-directional random selection can shorten the setup time.
The hydraulic index motor offers optimum service life.
Programmable tailstock
The tailstock on slide way gives maximum clamping stability.
The smooth tow along action is done by turret.
The hydraulic clamping to bed has variable hydraulic pressure to tailstock quill.
All tailstock movements are programmable bye M-code.
Direct Drive Mechanism
High precision preloaded ballscrews for reduced backlash.
Direct coupling eliminates motor backlash and improves torque transmission characteristics.
Absence of belt or gear drives removes transmission vibration. |
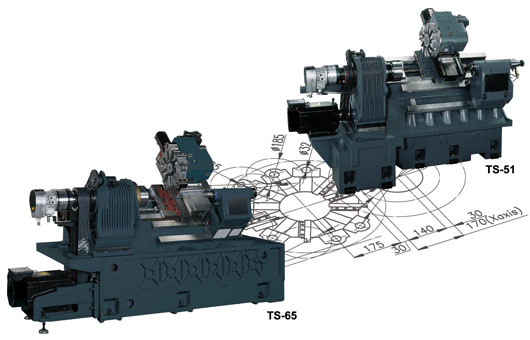
Quality Features Assure Greater Value! |
RIGIDITY... STABLITY... PRECISION... |
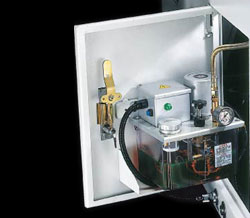 |
|
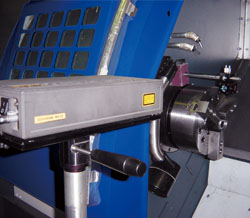 |
AUTOMATIC LUBRCATION SYSTEM |
|
LASTER INSPECTION |
The automatic lu-bricator provides lubrication toall slideways, ball screws and tail-stock ensures smooth motions atall times.
|
|
The CNC lathe has a standard hydraulic
chuck controlled by a foot switch for efficient
clamping of workpieces. |
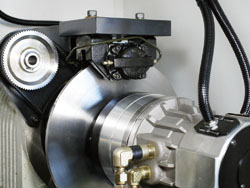 |
|
|
SPINDLE HYDRAULIC BRAKE |
|
|
The two steps hydraulic brake that can ensure the smooth C axis motion for machining in light braking force. The heavy braking can stop and take all the vibration from milling operations.
|
|
|
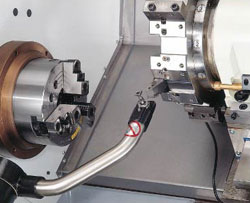 |
|
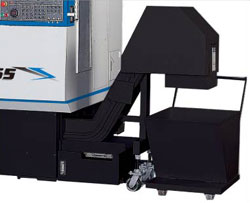 |
TOOL PRE-SETTER (option) |
|
CHIP CONVEYOR (option) |
The tool pre-setter effectively reduces
cutting tests while saving machining time.
The mechanism is used for measuring the
tool diameter and length.
The tool adjustment arm is powered and
program controlled.
|
|
The chip conveyor can bring the chips away
from the working area to avoid the thermal
effect of chips.
It saves the time for clean up the chips and
can be controlled by program. |
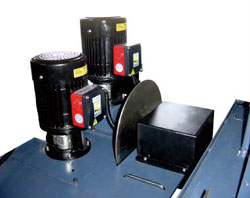 |
|
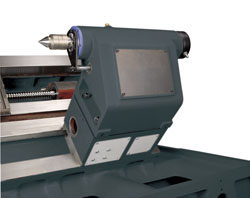 |
COOLANT SYSTEM & OIL /
WATER SEPARATOR (option) |
|
PROGRAMMABLE TAILSTOCK (option) |
High capacity designed coolant tank maintains
the coolant temperature.
The submerged type coolant pump delivers high
pressure coolant to flush chips and extend tool
service life.
High efficient disk type oil / water separator
provides quick oil / water separate (option). |
|
The ruggedly constructed, programmable
tailstock and quill movement can be
controlled on the control panel for easy
set-up and accurate positioning.
Tailstock movement is driven by turret slide. |
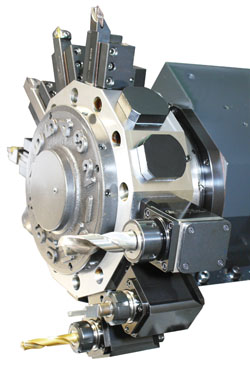 |
|
|
TURRETS |
|
|
VDI30, 12-Position power turret with AC servomotor.
Tool drive with spindle orientation.
Tools individually driven.
Radial tool mounting.
|
|
|
Easy Progmminng Teach-In Functions |
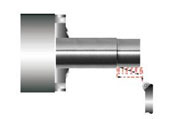 |
|
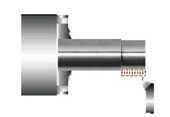 |
|
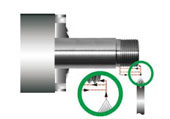 |
TURNING
(STRAIGHT AND TAPER) |
|
FACING
(STRAIGHT AND TAPER) |
|
THREADING
(STRAIGHT, TAPER AND MULTIPLE) |
Input the profile data from the blueprint. Press the simulation key to generate the graphic tool path. |
|
Input the specific parameters for this operation according to the graphic guide. |
|
For straight, taper or facial type of threads can be multiple as well. |
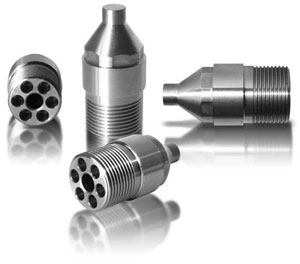 |
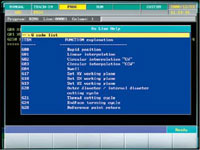 |
On-line help let the operator do programming
without any NC background. |
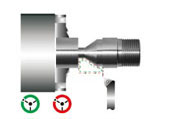 |
|
 |
|
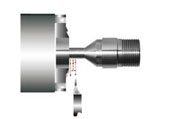 |
MPG SIMULATION |
|
END DRILLING |
|
GROOVING
(LONGITTUDINAL AND AXIAL) |
After the machining program is loaded, select the MPG mode to let the NC program be executed according to the MPG rotaion speed. |
|
Input the start, end point and drilling conditions to generate the NC program. |
|
Do both longitudinal and axial grooving combining roughing and finishing. |
TS Series Specifications |
( ) is the optional items |
|
Update, please look forward to. |
|
|
 |